The tyre industry is reducing the environmental impact of tyres with a circular approach to managing waste tyres and enhancing the performance of new tyres, according to Angelica Buan in this report.
A cocktail of chemicals in an old tyre
After microplastics found in products containing plastics, all eyes are now on end-of-life (ELT) rubber tyres, which are also found to be sources of microplastics and chemicals, including fillers, stabilisers, pigments, oils, resins, heavy metal additives and other compounds.
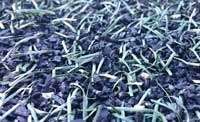
Crumb rubber granulate (CRG), produced from ELTs, for example, contains organic chemicals such as polyaromatic hydrocarbons (PAHs), phthalates, benzothiazoles, bisphenols and heavy metals, which can leach to the environment. This is a focus of the recent study done by the Norwegian Institute for Air Research (NILU), in collaboration with Akvaplan NIVA and Trondheim-based research organisation, SINTEF, on CRGs applied to artificial turfs used in playgrounds, running tracks and walkways in Norway.
The rubber crumbs are also releasing a cocktail of organic additives and metals into the marine environment. This included high concentrations of benzothiazole and zinc, as well as detectable levels of PAHs and phenolic compounds, the study stated. Co-project leader Dr Dorte Herzke also added that rubber from car tyres is found to be one of the largest contributors to microplastic pollution in the oceans. The study investigated CRG as being a potential seawater contaminant, and if it is toxic to marine organisms. Their tests involved exposing marine organisms to varying concentrations of CRG leachate to determine the toxic effects.
Meanwhile, what is clear is that car tyre rubber as well as CRGs contain massive amounts of filler systems (carbon black, clays, silicas, calcium carbonate), stabiliser systems (antioxidants, antiozonants, waxes), cross-linking agents (sulphur, accelerators, activators), and secondary components such as pigments, oils, resins and short fibres.
Also, chemical classes associated with car tyres include PAHs, phthalates, sulphenamides, guanidines, thiazoles, thiuams, dithiocarbamates, sulphur donors, phenolics, phenylenediamines and heavy metals. All of these substances, according to the authors of the NILU study, published in the Frontiers in Environmental Science, can have environmental impact and pose risks to human health.
Europe makes a case in circular recycling of ELTs
Each year, there are 26 million-1.6 billion tonnes of new tyres sold worldwide. This volume will eventually be scrapped and ideally, recycled. But a large portion still ends up in landfills or is incinerated.
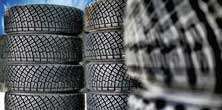
ELTs provide a significant amount of valuable materials for recovery. For proponents of circular economy, material recovery from ELTs will help the tyre industry greatly in its commitment to benefitting from the cost value of reusing the salvaged materials, while at the same time reducing their environment impact.
Europe is a model when it comes to recycling ELTs. The region, according to data from the European Tyre and Rubber Manufacturers’ Association (ETRMA), recycled 92% of ELTs collected and treated for material and energy recovery from 32 countries (EU28, Norway, Serbia, Switzerland and Turkey) in 2017. The secondary raw materials (SRM) from ELTs are utilised in industries such as construction, automotive and cement.
ELT recycling programmes have been created to propagate circular material recovery solutions. The EU-funded BlackCycle project will develop specific solutions to produce sustainable raw materials for tyres: ELT collection and feedstock selection, pyrolysis2 optimisation, oil refining and valorisation, furnace process optimisation, and sustainable tyre performance assessment.
The consortium is coordinated by French multinational tyre manufacturer Michelin together with seven industrial partners, five Research & Technological Organisations (RTOs) and five countries, including, France, Spain, Germany, Greece, and Switzerland.
The BlackCycle project, which started in May through to end of April 2023, aims at creating, developing, and optimising a full value chain from ELT feedstock to SRMs, with no waste of resources in any part of the chain and a specific attention for the environmental impact. These SRMs will be used to develop new ranges of passenger car and truck tyres, which will be sold commercially in European and global markets.
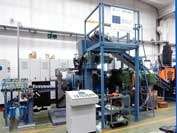
As a result, the BlackCycle value chain has a lower carbon footprint, emitting 0.93 kg/CO2/kg tyres less, and a lower use of fossil resources, using 0.89 kg fossil/kg ELT less. Moreover, BlackCycle will reduce the export of ELTs.
A previous EU-funded project, Rew-Tyres, focused on reclaiming clean de-vulcanised rubber from ELTs, enabling new tyres, and high-quality products. The three-year project was concluded in September 2019. The researchers of Rew-Tyres demonstrated two processes using prototype industrial machines.
The first process, called Rework, deals with rubber scraps from the tyre manufacturing process. Such scrap has been difficult to recycle because of the expensive and extremely energy-consuming machinery required, the researchers said. In Rework, scrap is treated in a gear pump and a mix-extruder, to produce sheets of homogeneous rubber. These can be directly reused in production. The process eliminates the energyhungry preheating stage, through a combination of compact gear design and the lubrication system. It is, thus, much more energy efficient than other rubber recycling processes, and more commercially viable, explains project coordinator, Florinda Martena.